ABOUT COMPRACK
We are comitted to be a preferred supplier for our customers who require innovative high performance trashrack solutions. We supply efficiency improving, corrosion-free, intake trashrack to the hydropower-, nuclear- and desalination-industry.
HISTORY
CompRack® has supplied trashrack in FRP (Fiber Reinforced Polymer) composite materials for almost 30 years. Our core competence is material and design know-how within FRP composite material applications. The first CompRack® trashrack system was developed in 1995 in close cooperation with the leading Swedish hydroelectric power producer Sydkraft (today E.ON). The objective was to develop a trashrack that combines a robust design with the highest possible level of efficiency.
At the beginning CompRack were introduced to a number of problems associated with conventional trashrack solutions. It soon became obvious that by introducing new material technology into the trashrack, it opened for a solution with superior properties in many areas. One of the areas to which special attention was paid during development process was ice, particularly frazil ice accumulation. CompRack’s low thermal conductivity combined with its hydraulic optimized geometry and surface properties has shown that the risk of frazil ice accumulation is significantly reduced.
Since the first CompRack FRP trashrack was delivered in 1995 we have continuously improved the product to be competitive and to add benefits for our customer within several areas.
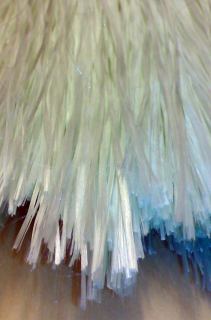
Glass fiber reinforcement
CompRack PROFILES
The CompRack profiles are made of FRP composite with a geometry and material mixture optimized for intake trashrack applications. Composites have been known and used for thousands of years. Since the 1950´s FRP composite materials have steadily gained ground in nearly all industrial sectors. Composites are defined as materials which consist of not less than two different material components, neither of which are well suited for construction purposes on their own, but which in combination result in a very strong and rigid material. Composites reinforced with long or continual fibres are often used in large structures such as ships, pressure tanks and aircrafts. The properties of the fibers are used to resist tensile and compressive loads, while the plastic – a specially formulated resin called the matrix material – transfers shear and also act as protection of the fibres. Because it is a combination of materials, a composite material can be combined and designed with a view to a specific purpose, in our case optimization of intake trashrack.
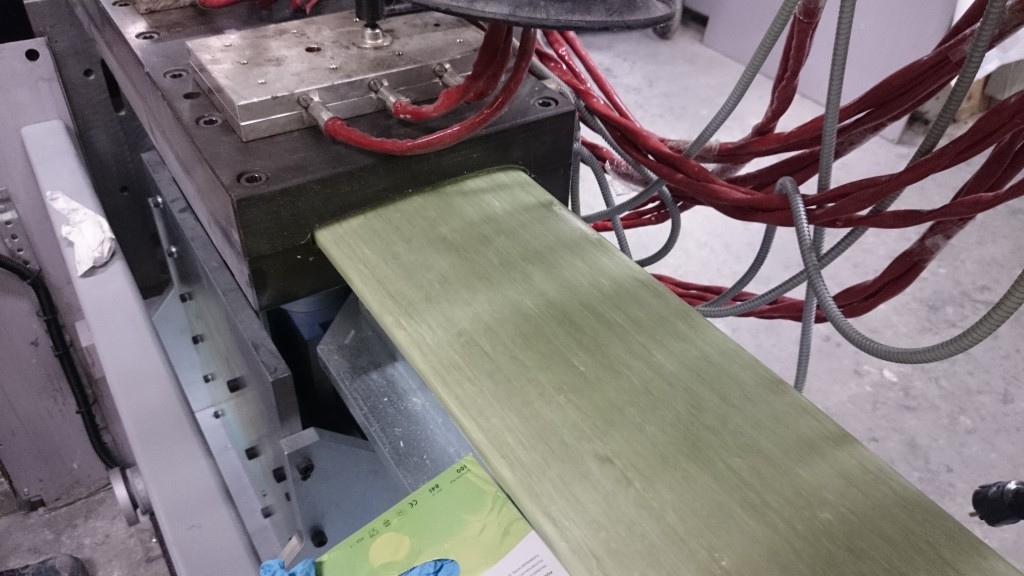
Pultruded CompRack profile
The CompRack FRP composite consists of two material components, glass fibers and a matrix based on a thermosetting polymer (Polyester, Vinylester or Polyurethane). The CompRack FRP composite material provides a number of benefits in relation to traditional materials. Two examples among others are resistance to corrosion and thermal insulating properties.
CompRack trashrack profiles are manufactured by pultrusion. The pultrusion process enables a continuous production of the composite profile with a cross sections and material properties tailored to our specifications. The method ensures consistent quality that can be reproduced time after time. The pultrusion takes place by continual fibers in roving or mat roving form being pulled through processing equipment where they are impregnated with the matrix material. Then the combined mixture of fibers and matrix is pulled on through the heated die where the profile is cured in its final geometry. The fully cured profile is then pulled forward to a flying saw which cuts the profiles into predefined lengths before it is forwarded to further preparation before assembly.
DESIGN
All CompRack trashrack solutions are designed to customer specifications, normally fully blocked trashrack with a specified maximum water level. This method of design results in a robust trashrack that will operate over a long period of time.
By using state of the art FEM-analysis system, accurate dimensioning is guaranteed. This computation covers stress, strain, buckling and structural resonance. We are capable of quickly and accurately analyze alternative solutions to find the most suitable solution for the intake in question.
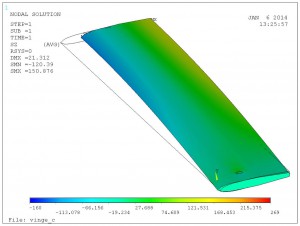
Stress and strain analysis
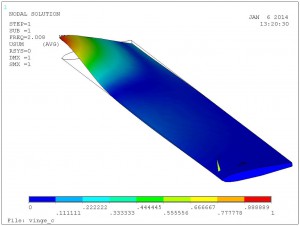
Buckling analysis
The profile has been optimized to get a minimum of obstruction of the flow, which results in a low energy Karman-vortex shedding = high efficiency profile. However all CompRack solutions have to pass through a FEM-analysis were the natural frequency of the trashrack is calculated, to ensure that no harmful vibrations will appear due to structural resonance. The natural frequency modes 1-3 shown in picture are compared to the emitted Karman vortex shedding frequency.
MANUFACTURING
When the CompRack trashrack profiles have been pultruded and cut into predefined length, metal parts manufactured, fasteners supplied, the assembly process takes place. The final preparation and assembly of profiles, spacers, and other parts forming the trashrack, is made in our workshop in Halmstad by our skilled personnel. A continuous quality control during the complete manufacturing and assembly process ensure that all products reaching our customers live up to the specifications. A quality- and dimensional- check of every product is also made as a final step before packing and shipping to the customer.
TRASHRACK EQUIPMENT READY FOR DELIVERY